SMARTFOLD 800RA ULTRA FOLDER GLUERS for beverage cartons Available widths:1100mm
|
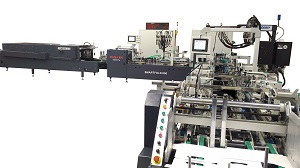
|
1. Feeder section
- Driven independently by servo motor and controlled by SmartServo.
- Friction feeder with 6 untimed feeding belts, 30 mm width.
- Electronic pile vibrator.
- Lateral feed gates fully adjustable to the width of the blank.
- Three adjustable front feed knives with carton spacing carriers (bogies).
- Motorized feed chains.
|
.jpg) .jpg)
|
2. Side register section
- Driven by SmartServo system.
- Independent section with an unparallel lower carrier that guides the box to a parallel handrail that allows a perfect blank alignment.
|
.jpg) |
3. Servo de-nicking via 3 independently controlled shafts
- Driven by SmartServo system.
- Three (3) precision timed de-nicking servo driven shafts with tooling
- Three (3) lower and upper carriers
|
.jpg) |
4. First folding section
- First folding section.
- Smooth and accurate folding of creases.
- Outer folding belts adjustable up to 180 degrees with variable speed.
- Two upper & two lower carriers with 25 mm lower and 30 mm outer belts.
|
.jpg) |
5. First Trombone section
- Driven independently by servo motor and controlled by Smartservo.
- Upper and lower drive mechanism for length adjustment.
- Equipped with automatic belt tension-adjusting system.
|
.jpg) |
6. Precision servo right angle blank transfer section - ServoTurn
- Driven by SmartServo system.
- Precision high speed timed right angle servo blank transfer.
- Easy setup for quick job changeover
|
.jpg) |
7. Final Folding & Closing section
- Driven by SmartServo system.
- Smooth and accurate folding of creases.
- Outer folding belts adjustable up to 180 degrees with variable speed.
- Two upper & two lower carriers with 25 mm lower and 30 mm outer belts.
|
.jpg)
|
8. Final Trombone section
- Driven independently by servo motor and controlled by Smartservo.
- Pneumatic box ejector, for quality control without interrupting the flow of boxes
- Upper and lower drive mechanism for length adjustment.
- Equipped with automatic belt tension-adjusting system.
- Continuous and automatic box collection mechanism that ensures a neat transfer to the Press section, guaranteeing a well aligned flow.
- Electronic counter and Kicker for marking batches.
|
.jpg) |
8.1. Trombone crushing rollers (Optional)
- Two (2) independently adjustable crushing rollers that can be positioned independently from the final fold carriers for precise positioning on the score as needed by the operator and carton design.
- Driven by the trombone SmartServo system.
- Independent pressure adjustment.
|
.jpg) |
9. Press section
- Driven independently by dual servo motors and controlled by SmartServo.
- Manual and Automatic speed variation in coordination with a photocell.
- Upper section moves back and forward, allowing for different box length.
- 5.5 meters total length with 3.1 meters effective pressure length.
- Pneumatic pressure adjustment to avoid marks.
- Squaring device for crashlock bottom boxes.
|
.jpg) .jpg)
|
10. SmartFeed Pre-feeder device (Optional)
- Lateral feed gates fully adjustable to the width of the blank.
- Two adjustable front feed knives with dual spring loaded feed rollers.
- Driven by adjustable variable drive system.
- Blank height in the folder gluer feeder section controlled by adjustable photocell.
- Two pneumatically activated back carton pile jogger/spankers for uniform pile integrity in the folder gluer feeder section.
- On wheels for easy positioning or removal.
- Can also be used on most folder gluers as a retrofit.
|
.jpg) |
11. Small conveyor post press (Optional)
- Small motorized 2 meter long belted conveyor after the press section.
- Adjustable back guide.
- Driven by adjustable variable drive system regulated with the folder gluer press section to change the shingle length for packing personnel.
- Quick electrical disconnect from the folder gluer for easy positioning and removal.
|
.jpg) |
|
|